The Future of Manufacturing: Electric Molding in Metal Fabrication
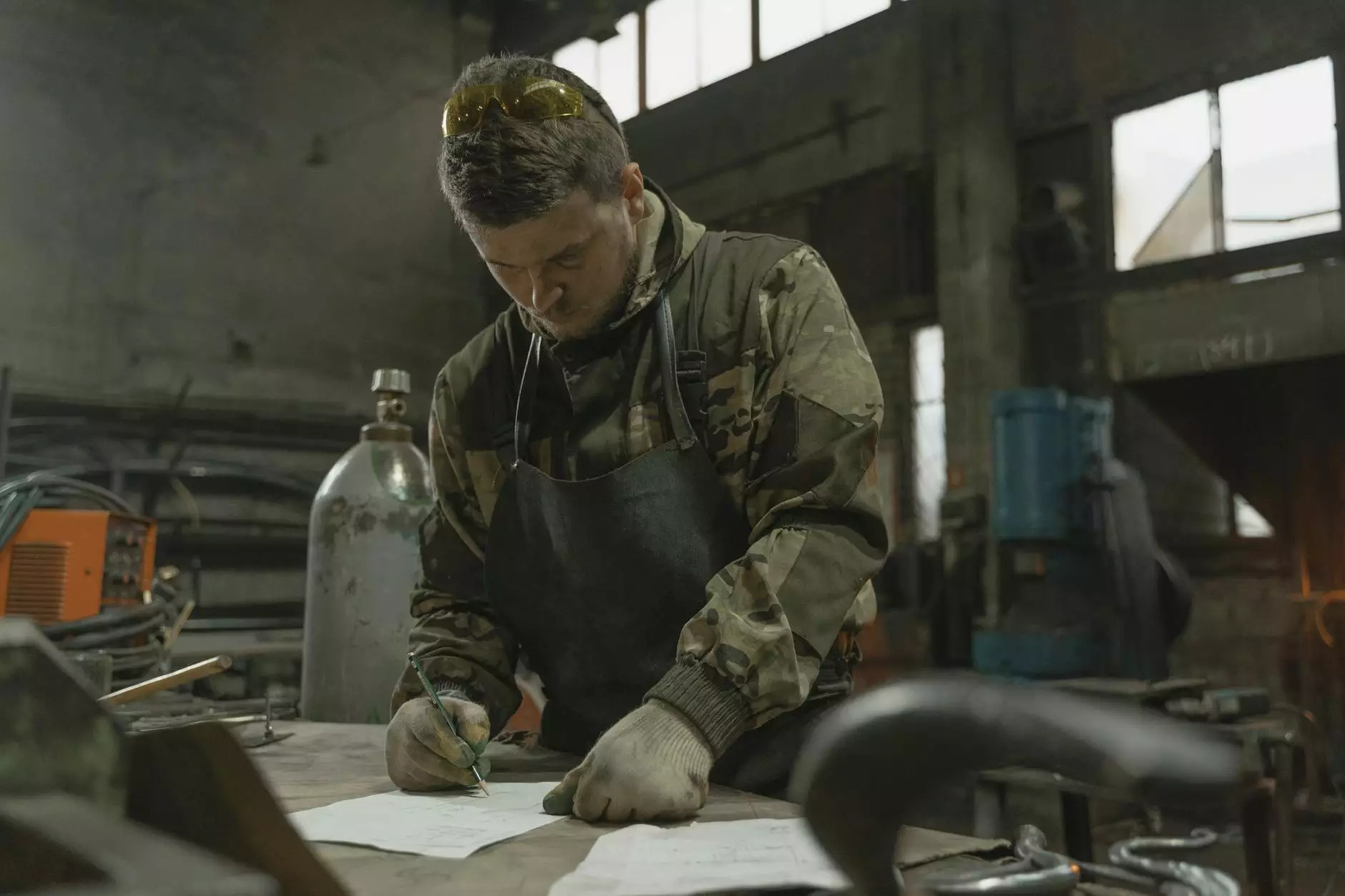
Introduction to Electric Molding
In today's fast-paced industrial landscape, the demand for precision and efficiency has led to the evolution of various manufacturing techniques. Electric molding, a cutting-edge technology in the realm of metal fabrication, stands as a testament to this evolution. This process combines electric energy with traditional molding methods to produce high-quality metal parts with enhanced precision and efficiency.
Understanding Electric Molding
Electric molding employs electric currents to heat and mold materials, primarily metals, into desired shapes. This method significantly improves the manufacturing process by enhancing the consistency and quality of the finished products.
The technology behind electric molding can be broken down into several key principles:
- Electric Resistance Heating: This technique uses electrical resistance to generate heat directly within the material, leading to enhanced efficiency.
- Temperature Control: Precise temperature regulation during the molding process ensures uniformity in the finished product.
- Reduced Cycle Times: Electric molding allows for quicker mold filling and cooling, thereby speeding up production.
Benefits of Electric Molding in Metal Fabricators
The integration of electric molding into the metal fabrication industry offers numerous advantages:
- Increased Precision: Electric molding technology allows for tighter tolerances and improved dimensional accuracy in metal parts, crucial for high-performance applications.
- Enhanced Efficiency: The rapid heating and cooling processes associated with electric molding reduce production times, allowing manufacturers to meet tight deadlines.
- Energy Savings: Compared to traditional molding methods, electric molding offers significant reductions in energy consumption, contributing to a more sustainable operation.
- Improved Surface Finish: This method can produce parts with superior surface quality, minimizing the need for additional machining or finishing processes.
Applications of Electric Molding in Metal Fabrication
Electric molding finds a diverse range of applications across various industries. Some of the key sectors utilizing this technology include:
- Aerospace: Precision components that meet stringent safety and performance standards.
- Automotive: High-strength and lightweight parts that enhance vehicle performance and fuel efficiency.
- Electronics: Components requiring intricate designs and high levels of reliability.
- Medical Devices: Precision engineering for life-saving devices that demand exacting standards.
How to Implement Electric Molding in Your Manufacturing Process
Transitioning to electric molding requires careful planning and execution. Here are some steps to consider:
- Assessment of Current Capabilities: Evaluate your existing molding processes and identify areas where electric molding can bring enhancements.
- Training Personnel: Ensure your workforce is adequately trained in using electric molding technology to maximize its benefits.
- Invest in Equipment: Procure electric molding machines that align with your production needs and capacity.
- Continuous Improvement: Regularly assess the performance of electric molding processes and seek opportunities for further optimization.
The Future of Electric Molding in Metal Fabrication
The future of electric molding in metal fabrication looks promising as technological advancements continue to emerge. With ongoing research and development, we can expect enhancements in:
- Automation: Increased automation will streamline the molding process, reducing labor costs and minimizing human error.
- Smart Manufacturing: Integration with IoT (Internet of Things) will allow for real-time monitoring and adjustments, leading to more efficient production.
- Sustainability: Green technologies are expected to further reduce energy consumption and waste in the electric molding process.
Conclusion: Embracing Electric Molding for Competitive Advantage
In conclusion, electric molding represents a significant leap forward in the field of metal fabrication. Its numerous benefits, ranging from improved precision and efficiency to significant energy savings, make it an appealing option for businesses looking to enhance their manufacturing capabilities. By embracing this innovative technology, companies can not only improve their process but also gain a crucial competitive advantage in today's demanding marketplace.
For those interested in exploring electric molding, Deep Mould, a leader in the field of metal fabrication, offers state-of-the-art solutions tailored to meet a variety of industrial needs. By partnering with experts, businesses can unlock the full potential of electric molding and drive their success in the industry.