Understanding Lathe Machining Parts: A Comprehensive Overview
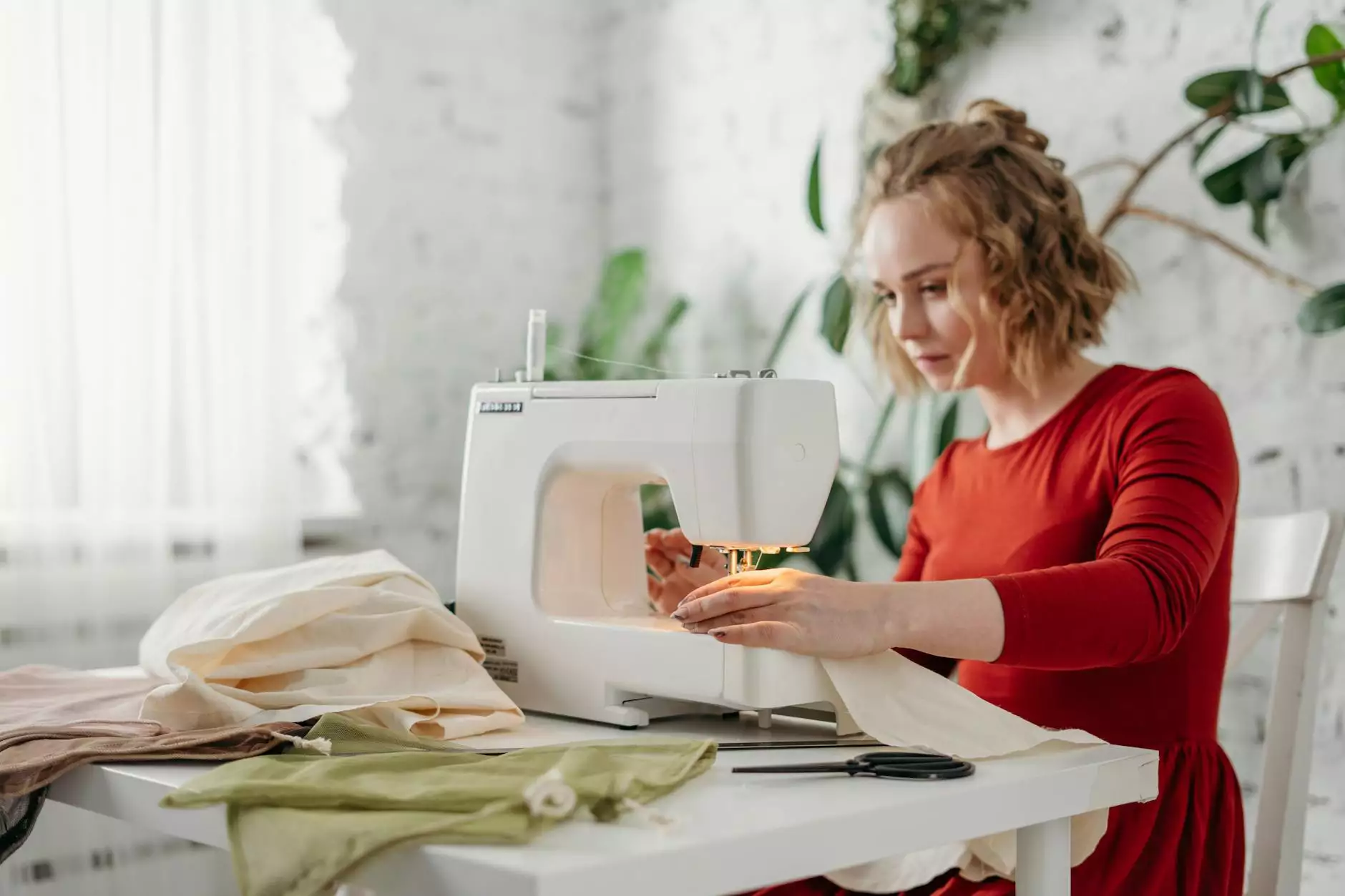
Lathe machining parts are critical components in various industries, including aerospace, automotive, and industrial manufacturing. These parts are created using lathes—machines that rotate the workpiece against a cutting tool. This process results in high precision and excellent finish quality, making lathe machining an essential technique in metal fabrication. In this article, we will explore the intricacies of lathe machining, the types of parts produced, and their numerous applications.
The Process of Lathe Machining
The lathe machining process involves several key steps:
- Setup: Proper setup of the lathe and the workpiece is crucial. The material is mounted on the lathe, and the cutting tools are prepared.
- Turning: As the lathe operates, the workpiece is rotated while cutting tools remove material to achieve the desired shape and size.
- Finishing: This step involves polishing and refining the surface to ensure it meets specific quality standards.
- Quality Control: Finally, the finished part undergoes rigorous inspection to guarantee precision and quality before it is delivered to the client.
The Importance of Quality in Lathe Machining Parts
In sectors where precision is paramount, the quality of lathe machining parts can significantly impact overall performance. Flaws in these components can lead to:
- Reduced efficiency in machinery.
- Increased likelihood of wear and tear.
- Potential safety hazards in operational environments.
Applications of Lathe Machining Parts
Lathe machining parts are ubiquitous across various sectors. Some notable applications include:
Aerospace Industry
The aerospace industry relies on lathe machining parts for components such as turbine blades, engine housings, and landing gear. Precision and reliability are critical here, and high-quality machined parts meet the stringent standards required for flight safety.
Automotive Industry
In automotive manufacturing, lathe machining is essential for producing engine components, transmission parts, and axle assemblies. These parts must endure extreme conditions, making the quality of lathe machining imperative for vehicle performance and longevity.
Medical Equipment
Lathe machining plays a vital role in the production of surgical instruments and medical devices. The precision of lathe machined parts ensures that instruments perform effectively and safely, ultimately contributing to patient care.
Key Features of Quality Lathe Machining Parts
When considering lathe machining parts, several features denote quality:
- Precision: High levels of accuracy are required to ensure proper fit and function.
- Surface Finish: A smooth finish not only improves aesthetics but also reduces friction and wear.
- Material Selection: The choice of material affects durability and performance. Common materials include aluminum, steel, and titanium.
- Consistency: Consistent quality across multiple parts is essential for manufacturability and reliability.
Choosing a Reliable Supplier for Lathe Machining Parts
When selecting a supplier for your lathe machining parts, consider the following criteria to ensure you receive high-quality products:
Experience and Reputation
Choose a supplier with a strong industry reputation and extensive experience. A company like deepmould.net has established itself as a leader in the field, known for superior quality and precision.
Technological Capabilities
Modern lathes equipped with advanced technology can produce more complex geometries with higher efficiency. Ensure your supplier invests in up-to-date machinery and techniques.
Quality Assurance Processes
A reputable supplier will have rigorous quality control measures in place, including testing and inspection protocols to maintain high standards throughout the manufacturing process.
Customization Options
Look for a supplier that offers customization to meet your specific needs. This flexibility can significantly enhance your production capabilities.
Future Trends in Lathe Machining
The future of lathe machining is being shaped by several innovative trends:
Smart Manufacturing
The integration of IoT (Internet of Things) in lathe machining allows for real-time monitoring and data collection, leading to improved efficiencies and predictive maintenance.
Automation
Advancements in automation technologies, such as robotic arms and CNC lathes, are streamlining production processes and reducing human error, ensuring uniformity in lathe machining parts.
Sustainability
With increasing attention to environmental issues, companies are focusing on sustainable practices, including waste reduction and sourcing materials responsibly. This trend is becoming crucial in attracting clients who value corporate responsibility.
Conclusion
In conclusion, understanding lathe machining parts and their production process is essential for industries reliant on precision components. With their widespread application in sectors like aerospace, automotive, and medical fields, the demand for high-quality lathe machining is clear. Choosing a trusted supplier like deepmould.net can assure you of receiving reliable, durable, and precision-engineered parts that meet your specific performance needs.
As technology evolves, the integration of smart manufacturing and sustainable practices will shape the future of lathe machining, making it an exciting area of exploration for businesses aiming to thrive in an increasingly competitive market.